• ATHOS ASSESSORIA E TREINAMENTOS
Abaixo estão os serviços prestados pela Athos
Com anos de experiência no mercado, a Athos garante qualidade, variedade e o melhor atendimento para nossos clientes.
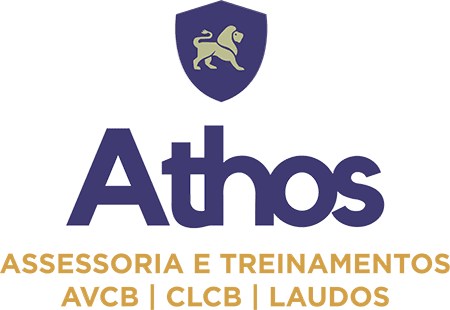
A Permissão de Trabalho de Alto Risco é um documento exigido em várias atividades que envolvem riscos significativos à segurança e à saúde dos trabalhadores, como serviços em altura, trabalhos com eletricidade, operações com máquinas pesadas, trabalhos em espaços confinados, entre outros.
Principais Documentos Necessários:
Análise de Risco: Relatório identificando os possíveis riscos e medidas de controle.
Plano de Trabalho: Descrição detalhada das atividades a serem realizadas.
Permissão de Trabalho (PT): Documento que autoriza a execução do serviço de alto risco.
Treinamento e Certificações: Certificados que comprovem a capacitação dos trabalhadores (NR-10, NR-33, NR-35, etc.).
Ficha de Equipamentos de Proteção Individual (EPI): Relação dos EPIs utilizados, com comprovação de entrega e treinamento.
Laudos Técnicos e Inspeções: Como laudos elétricos, de estabilidade e de integridade estrutural.
Autorização do Responsável Técnico: Assinatura do engenheiro ou responsável técnico pela atividade.
Documentação dos Trabalhadores: Carteira de Trabalho, exames médicos e comprovantes de capacitação.
Exemplos de Situações que Exigem Permissão:
Trabalhos em altura (NR-35).
Trabalhos em espaços confinados (NR-33).
Atividades com eletricidade (NR-10).
Operação de máquinas e equipamentos pesados (NR-12).
Manuseio de produtos químicos perigosos (NR-20).
O Programa de Gerenciamento de Riscos (PGR) é um documento obrigatório em diversas empresas, conforme estabelecido pela NR-01 (Norma Regulamentadora nº 1), que trata da Gestão de Riscos Ocupacionais. O objetivo principal do PGR é identificar, avaliar e controlar os riscos presentes no ambiente de trabalho, garantindo a saúde e segurança dos trabalhadores.
Principais Componentes do PGR:
Inventário de Riscos:
Identificação dos perigos e riscos associados às atividades.
Classificação dos riscos (físicos, químicos, biológicos, ergonômicos e de acidentes).
Avaliação da magnitude dos riscos.
Plano de Ação:
Medidas de prevenção e controle dos riscos identificados.
Definição de responsabilidades e prazos para implementação.
Monitoramento e revisão periódica das ações adotadas.
Documentação e Registros:
Fichas de EPIs e EPCs utilizados.
Registros de inspeções, manutenção e treinamentos realizados.
Protocolos de investigação de acidentes e incidentes.
Treinamento e Capacitação:
Programas educativos para orientar os trabalhadores sobre os riscos e as medidas de prevenção.
Capacitação para uso correto de equipamentos de proteção.
Monitoramento e Avaliação:
Acompanhamento contínuo da eficácia das medidas adotadas.
Revisão periódica do programa para atualização e melhorias.
Importância do PGR:
O PGR é fundamental para garantir a integridade física e mental dos trabalhadores, prevenindo acidentes e doenças ocupacionais. Além disso, ele demonstra o comprometimento da empresa com as normas de saúde e segurança, evitando penalidades legais.
A NR-12 (Norma Regulamentadora nº 12) trata da Segurança no Trabalho em Máquinas e Equipamentos, com o objetivo de garantir a segurança e a saúde dos trabalhadores que operam ou interagem com máquinas e equipamentos. Ela estabelece diretrizes sobre a instalação, operação, manutenção e treinamento necessários para evitar acidentes e proteger a integridade dos colaboradores.
Um Projeto de Adequação à NR-12 visa garantir que todas as máquinas e equipamentos da empresa estejam de acordo com os requisitos de segurança estabelecidos pela norma. Abaixo está o passo a passo para elaborar esse projeto:
Estrutura de um Projeto de Adequação à NR-12
1. Levantamento de Máquinas e Equipamentos
Identificação: Listar todas as máquinas e equipamentos que são utilizados na empresa.
Avaliação de Riscos: Realizar uma análise de risco para cada máquina ou equipamento, considerando os perigos potenciais (mecânicos, elétricos, ergonômicos, etc.).
2. Análise e Diagnóstico
Conformidade: Verificar se as máquinas estão em conformidade com os requisitos da NR-12, como proteção contra partes móveis, dispositivos de segurança, sistemas de bloqueio e sinalização de risco.
Pontuação dos Itens de Não Conformidade: Identificar quais itens da norma não estão sendo atendidos e a gravidade de cada não conformidade.
3. Plano de Adequação
Propostas de Correção: Descrever as ações necessárias para adequação, como a instalação de proteções, dispositivos de segurança (botões de emergência, sensores, etc.), melhorias no treinamento e operação, e modificações nas máquinas.
Priorização: Determinar a ordem de implementação das melhorias, priorizando máquinas e processos com maior risco de acidente.
4. Projetos Técnicos e Execução
Modificações Técnicas: Elaborar projetos técnicos para a adequação das máquinas, com base nas diretrizes da NR-12.
Fases de Implementação: Definir o cronograma de execução das adequações, incluindo compra de equipamentos de proteção, instalação e modificações nas máquinas.
Responsabilidade Técnica: Nomear engenheiros ou profissionais qualificados para a execução das modificações e garantir a conformidade com a norma.
5. Treinamento e Capacitação
Treinamento de Funcionários: Oferecer cursos de capacitação sobre o uso seguro das máquinas e equipamentos, considerando as mudanças feitas para atender à NR-12.
Instruções de Operação: Criar e distribuir manuais de operação segura, informando sobre os novos dispositivos de segurança e procedimentos a serem seguidos.
6. Acompanhamento e Monitoramento
Inspeções Regulares: Estabelecer um calendário de inspeções para garantir que as adequações estejam sendo mantidas ao longo do tempo.
Avaliação de Desempenho: Avaliar a eficácia das ações implementadas e fazer ajustes quando necessário.
7. Documentação Final
Relatório Final de Adequação: Elaborar um relatório técnico detalhado, contendo o diagnóstico inicial, as ações implementadas e a situação final das máquinas e equipamentos.
Certificação de Conformidade: Emitir um documento de conformidade com a NR-12, atestando que todas as máquinas estão adequadas às exigências de segurança.
Importância do Projeto de Adequação à NR-12
A adequação às normas de segurança da NR-12 não só protege a vida e a saúde dos trabalhadores, mas também evita multas e processos administrativos. Além disso, ela contribui para aumentar a produtividade, pois as máquinas passam a operar de maneira mais segura e eficiente, reduzindo o número de acidentes e paradas inesperadas.
O Projeto de Linha de Vida e Ponto de Ancoragem é uma exigência da NR-35 (Norma Regulamentadora nº 35), que trata da Segurança no Trabalho em Altura. A NR-35 estabelece requisitos para garantir a segurança dos trabalhadores que executam atividades em altura, como a instalação de sistemas de proteção, linhas de vida e pontos de ancoragem para evitar quedas e outros acidentes.
Estrutura do Projeto de Linha de Vida e Ponto de Ancoragem
1. Objetivo do Projeto
O projeto visa garantir a segurança dos trabalhadores que atuam em altura, oferecendo meios adequados de prevenção contra quedas. As linhas de vida e os pontos de ancoragem devem ser planejados e executados de forma a garantir a eficácia no sistema de proteção.
2. Análise Inicial e Levantamento de Riscos
Avaliação do Local: Levantar as características do local onde será realizada a atividade em altura (ex: telhados, andaimes, plataformas, etc.).
Identificação dos Riscos: Identificar os riscos de queda e outros acidentes associados ao trabalho em altura, considerando a altura, a complexidade do trabalho e os possíveis obstáculos.
Pontos Críticos: Identificar os pontos de maior risco e onde será necessário o uso de sistemas de proteção.
3. Definição dos Sistemas de Proteção
Linha de Vida: Sistema contínuo de ancoragem, composto por cabos, cordas ou trilhos, ao longo dos quais o trabalhador se prende com o equipamento de proteção individual (EPI).
Pontos de Ancoragem: São os locais específicos onde o trabalhador irá se fixar (normalmente com cinto de segurança e talabarte). Esses pontos devem ser projetados para suportar a carga do trabalhador em caso de queda.
Tipos de Linhas de Vida:
Horizontal: Para longos trajetos em que o trabalhador precisa se mover ao longo da estrutura.
Vertical: Usado em áreas onde o trabalhador sobe ou desce, como em escadas ou torre.
Mista: Combinação dos dois tipos, dependendo da natureza da atividade.
4. Projeto Técnico da Linha de Vida e Ponto de Ancoragem
Cálculos Estruturais: O projeto deve incluir cálculos que garantam que os pontos de ancoragem e as linhas de vida suportem as forças envolvidas, levando em consideração o peso do trabalhador, o impacto de uma possível queda e os fatores ambientais (como vento ou condições climáticas).
Especificações dos Materiais: Definir os materiais a serem utilizados (cabo de aço, cordas, suportes, ancoragens, etc.), com base na resistência necessária e nas normas técnicas vigentes.
Distribuição e Posicionamento: Determinar a posição estratégica dos pontos de ancoragem e da linha de vida, levando em conta a movimentação do trabalhador e a facilidade de acesso.
5. Instalação e Execução
Procedimentos de Instalação: Estabelecer as etapas de instalação da linha de vida e dos pontos de ancoragem, incluindo a fixação dos suportes, o tensionamento das linhas e a verificação da resistência.
Equipamentos de Proteção: Orientar sobre os Equipamentos de Proteção Individual (EPIs) a serem utilizados, como cintos de segurança, talabartes e capacetes.
Testes e Ensaios: Após a instalação, realizar testes de resistência para verificar se a linha de vida e os pontos de ancoragem estão adequadamente posicionados e seguros.
6. Treinamento dos Trabalhadores
Capacitação: Oferecer treinamento adequado para todos os trabalhadores que irão utilizar os sistemas de proteção, abordando como utilizar a linha de vida e os pontos de ancoragem de maneira segura.
Instruções de Uso: Fornecer manuais de instrução detalhados para o uso correto dos EPIs e dos sistemas de segurança.
7. Manutenção e Inspeções
Inspeções Periódicas: Realizar inspeções regulares para garantir a integridade dos pontos de ancoragem e das linhas de vida. Isso inclui verificar desgaste, corrosão ou outros danos nos materiais.
Plano de Manutenção: Estabelecer um plano de manutenção preventiva e corretiva para os sistemas de ancoragem e linhas de vida.
8. Documentação e Registro
Relatório Técnico: Elaborar um relatório técnico detalhado com todos os cálculos, materiais, desenhos e especificações do projeto.
Certificado de Conformidade: Emitir um certificado atestando que o sistema de proteção está em conformidade com as normas da NR-35 e demais exigências de segurança.
Importância do Projeto de Linha de Vida e Ponto de Ancoragem
A correta implementação de linhas de vida e pontos de ancoragem é essencial para evitar quedas, que são uma das principais causas de acidentes no trabalho em altura. Além disso, esse projeto é uma exigência legal, e sua implementação contribui para a segurança dos trabalhadores, evitando multas, danos e prejuízos à saúde e à integridade física dos colaboradores.
O Prontuário das Instalações Elétricas é um documento técnico exigido pela NR-10 (Norma Regulamentadora nº 10), que trata da Segurança em Instalações e Serviços em Eletricidade. Esse prontuário tem como objetivo reunir toda a documentação relacionada à instalação elétrica de um ambiente ou empresa, garantindo que ela esteja em conformidade com as normas de segurança, tanto para a prevenção de acidentes quanto para a manutenção das condições ideais de operação.
A seguir, estão os componentes principais do Prontuário das Instalações Elétricas:
Conteúdo do Prontuário das Instalações Elétricas
1. Identificação da Empresa ou Instalação
Razão Social: Nome completo da empresa.
CNPJ: Cadastro Nacional da Pessoa Jurídica.
Endereço da Instalação: Local onde o prontuário está sendo elaborado.
Responsável Técnico: Nome do engenheiro eletricista ou responsável técnico que elaborou e assinou o projeto e os documentos.
2. Projeto da Instalação Elétrica
Memorial Descritivo: Descrição detalhada do projeto elétrico, especificando as características gerais da instalação, como tipo de alimentação, layout das instalações, e demais informações técnicas.
Esquemas Unifilares: Representação gráfica da instalação elétrica, que mostra as ligações entre os principais componentes, como transformadores, disjuntores, circuitos e barramentos.
Esquemas de Aterramento e Equipotencialização: Diagramas que mostram os sistemas de aterramento da instalação, fundamentais para garantir a segurança contra choques elétricos.
Quadros de Distribuição: Descrição e localização dos quadros de distribuição elétrica e suas características (como amperagem e circuitos).
3. Relatório de Inspeção e Manutenção
Inspeções Regulares: Relatórios sobre inspeções realizadas nas instalações elétricas, de acordo com as exigências da NR-10, que garantem o bom funcionamento e a segurança da instalação elétrica.
Laudos de Manutenção: Relatórios sobre os serviços de manutenção preventiva e corretiva realizados, incluindo a troca de equipamentos, verificação de conexões e demais ajustes técnicos.
Controle de Não Conformidades: Identificação de problemas ou falhas detectadas durante as inspeções e as ações corretivas tomadas para solucioná-los.
4. Certificados de Equipamentos
Certificação de Equipamentos e Materiais: Certificados de conformidade dos equipamentos e materiais utilizados na instalação elétrica, como disjuntores, cabos, fiação, transformadores, entre outros.
Laudos de Equipamentos de Proteção: Laudos de testes dos dispositivos de proteção (como disjuntores, relés de proteção, etc.) e equipamentos de segurança (como aterramento e sistemas de proteção contra choques).
5. Procedimentos de Segurança
Procedimentos Operacionais: Manual com instruções detalhadas sobre como operar, manter e realizar manutenções nas instalações elétricas, incluindo os cuidados com a segurança.
Plano de Emergência: Estratégias a serem seguidas em caso de acidente ou falha na instalação elétrica, como o desligamento rápido, acionamento de segurança e primeiros socorros.
6. Treinamento e Capacitação
Registros de Treinamento: Documentação que comprova que os trabalhadores que operam ou realizam manutenção nas instalações elétricas foram treinados conforme as exigências da NR-10, com os certificados de capacitação.
Periodicidade dos Treinamentos: Descrição da periodicidade com que os treinamentos de segurança são realizados, conforme a necessidade de reciclagem dos funcionários.
7. Análise de Riscos e Avaliação de Perigos
Identificação de Riscos: Relatório sobre os riscos elétricos envolvidos nas instalações, como choques elétricos, incêndios, explosões, entre outros.
Plano de Controle de Riscos: Medidas adotadas para minimizar ou eliminar os riscos identificados, como sistemas de aterramento, proteções contra sobrecarga e curto-circuito, dispositivos de desligamento de emergência, etc.
8. Documentação Adicional
Autorização para Trabalhos em Instalações Elétricas: Documentos que autorizam os trabalhadores a realizarem intervenções ou manutenções nas instalações elétricas, conforme as normas de segurança.
Ficha de EPI (Equipamento de Proteção Individual): Ficha de registro de todos os EPIs fornecidos aos trabalhadores e que são obrigatórios para a realização de atividades em instalações elétricas.
9. Plano de Ações Corretivas
Relatório de Acidentes ou Incidentes: Caso haja qualquer acidente ou incidente relacionado à instalação elétrica, deve haver o devido registro, investigação das causas e ações corretivas tomadas.
Plano de Melhoria: Estratégias e ações para melhorar as condições de segurança nas instalações elétricas, com base nas auditorias, inspeções e feedback dos trabalhadores.
Importância do Prontuário das Instalações Elétricas
O Prontuário das Instalações Elétricas é essencial para garantir que as instalações elétricas estejam de acordo com as exigências legais e normas de segurança, como a NR-10. Ele ajuda a prevenir acidentes, proporciona rastreabilidade e controle sobre a manutenção e segurança da instalação, e também serve como referência para auditorias e inspeções regulatórias.
Além disso, o prontuário assegura que a empresa esteja preparada para enfrentar situações de emergência, esteja conforme a legislação vigente, e consiga oferecer aos seus colaboradores um ambiente de trabalho seguro.
A termografia em instalações elétricas é uma técnica de inspeção não invasiva que utiliza câmeras térmicas para detectar e medir a temperatura de componentes elétricos, como cabos, conexões, disjuntores e equipamentos em funcionamento. Essa técnica é extremamente útil para identificar pontos de sobrecarga, falhas de isolamento, conexões frouxas ou desgastadas, e outros problemas que podem gerar riscos de curto-circuitos ou incêndios.
A NR-10 (Segurança em Instalações e Serviços em Eletricidade) recomenda a utilização de inspeções regulares, e a termografia é uma das ferramentas recomendadas para garantir a segurança e a eficiência das instalações elétricas.
Benefícios da Termografia em Instalações Elétricas
Detecção Precoce de Problemas
A termografia permite identificar problemas antes que se tornem falhas catastróficas, como conexões frouxas, sobrecarga, e aquecimento excessivo de componentes. Isso pode prevenir incêndios e danos a equipamentos caros.Monitoramento Contínuo
A inspeção térmica pode ser realizada sem interromper a operação da instalação, o que significa que você pode monitorar em tempo real e sem comprometer o funcionamento da planta ou instalação.Segurança Melhorada
Detectar pontos quentes ou falhas em sistemas elétricos ajuda a evitar acidentes elétricos, como choques e incêndios, aumentando a segurança para os trabalhadores e para as instalações.Aumento da Vida Útil dos Equipamentos
Ao identificar falhas precoces e corrigi-las a tempo, é possível prolongar a vida útil dos equipamentos elétricos, evitando reparos caros ou substituições prematuras.Eficiência Energética
A termografia ajuda a identificar pontos de resistência nos circuitos, o que pode resultar em perdas de energia. Com isso, é possível melhorar a eficiência energética da instalação.
Como Funciona a Termografia em Instalações Elétricas
Equipamento Utilizado:
Câmeras Termográficas: São câmeras especiais equipadas com sensores infravermelhos capazes de capturar imagens térmicas dos componentes elétricos. Essas câmeras exibem as imagens em uma escala de cores, onde as áreas mais quentes geralmente aparecem em cores mais quentes (vermelho ou amarelo) e as áreas mais frias em cores mais frias (azul ou verde).
Processo de Inspeção:
A câmera térmica é direcionada para os componentes elétricos enquanto eles estão em operação. A câmera detecta e mapeia a temperatura de diferentes áreas e peças.
O profissional responsável pela inspeção analisa a imagem térmica em tempo real para identificar quaisquer pontos quentes anormais ou irregularidades na distribuição de calor.
A detecção de temperaturas elevadas em componentes pode indicar problemas como conexões soltas, falhas de isolamento, sobrecarga ou curto-circuitos iminentes.
Identificação de Problemas Comuns:
Conexões Elétricas Frouxas: A termografia pode identificar pontos de calor excessivo em conexões frouxas, o que indica que há resistência e, consequentemente, um risco de falha.
Cabos Superaquecendo: Se os cabos estiverem superaquecendo devido a sobrecarga ou fiação inadequada, a câmera térmica pode identificar essas áreas quentes.
Disjuntores e Fusíveis Defeituosos: A inspeção térmica pode detectar falhas em disjuntores e fusíveis que não estão funcionando adequadamente.
Falta de Aterramento ou Aterramento Deficiente: Problemas no aterramento de sistemas podem resultar em altas temperaturas e serem identificados através da termografia.
Passos para Realizar uma Inspeção Termográfica em Instalações Elétricas
Planejamento da Inspeção:
Identificar os pontos críticos da instalação elétrica, como quadros de distribuição, disjuntores, cabos e conexões.
Planejar a inspeção de acordo com as condições operacionais da instalação, preferencialmente quando os equipamentos estiverem sob carga normal de operação.
Realização da Inspeção:
Utilizar a câmera térmica para capturar as imagens térmicas de todos os pontos críticos.
Observar os resultados em tempo real e identificar pontos quentes anormais.
Análise dos Resultados:
Após a inspeção, analisar as imagens térmicas e comparar as temperaturas detectadas com os parâmetros aceitáveis para cada componente.
Identificar possíveis problemas e falhas com base nas imagens térmicas, e documentar as áreas que precisam de atenção.
Relatório Técnico:
Elaborar um relatório detalhado, com as imagens térmicas e a interpretação dos dados, destacando as áreas com falhas detectadas e recomendando as ações corretivas.
Ações Corretivas:
Com base no relatório, realizar as correções necessárias, como apertar conexões, substituir componentes defeituosos ou ajustar a carga elétrica.
Recomendações de Frequência de Inspeções Termográficas
Inspeções Periódicas: Para instalações elétricas críticas, é recomendada a realização de inspeções termográficas a cada 6 meses ou, no máximo, uma vez por ano.
Inspeções Após Modificações: Sempre que houver modificações na instalação elétrica, como a adição de novos equipamentos ou mudanças na carga elétrica, é importante realizar uma nova inspeção termográfica.
Durante Eventos Críticos: Caso haja falhas recorrentes ou aumento de consumo, uma inspeção adicional deve ser realizada para prevenir danos maiores.
Conclusão
A termografia é uma ferramenta extremamente eficaz e prática para garantir a segurança das instalações elétricas. Ela ajuda a identificar problemas antes que se tornem falhas catastróficas, prevenindo acidentes, danos aos equipamentos e melhorando a eficiência energética. A realização de inspeções regulares, especialmente em ambientes críticos, é essencial para manter as condições ideais de operação e segurança.
O Teste de Arrancamento Estático em pontos de ancoragem é uma prática essencial para garantir a segurança dos sistemas de ancoragem utilizados em trabalhos em altura, conforme exigido pela NR-35 (Segurança no Trabalho em Altura) e outras normas técnicas. Esse teste tem como objetivo verificar a resistência e a confiabilidade dos pontos de ancoragem, assegurando que eles suportem a carga máxima que pode ser exercida durante uma possível queda ou esforço excessivo.
O que é o Teste de Arrancamento Estático?
O teste de arrancamento estático é realizado para medir a capacidade de um ponto de ancoragem de resistir à força de tração (ou arrancamento) sem sofrer falhas. Esse teste simula uma situação em que o ponto de ancoragem seria submetido a uma carga máxima (geralmente equivalente ao peso de um trabalhador em queda) para verificar se ele pode suportar essa força sem se soltar ou comprometer a segurança.
Objetivo do Teste de Arrancamento Estático
Verificar a Estabilidade do Ponto de Ancoragem: Garantir que o ponto de ancoragem (seja um gancho, olho de ferro, estrutura metálica ou outro tipo) seja capaz de suportar a carga que o trabalhador exerce durante uma queda ou força excessiva sem que ocorra seu descolamento ou falha.
Testar a Integridade do Sistema de Ancoragem: Avaliar a qualidade da instalação e do ponto de ancoragem, garantindo que ele esteja adequadamente fixado e que os materiais utilizados sejam os adequados e sem defeitos.
Prevenir Acidentes: Com a realização do teste, evita-se falhas nas ancoragens que podem resultar em quedas acidentais durante o trabalho em altura, minimizando os riscos à segurança do trabalhador.
Procedimento para Realizar o Teste de Arrancamento Estático
O teste de arrancamento estático deve ser realizado de maneira cuidadosa e seguindo algumas etapas:
1. Planejamento e Preparação
Identificação do Ponto de Ancoragem: O ponto a ser testado deve ser cuidadosamente identificado. Pode ser uma estrutura existente, um ponto de ancoragem novo ou qualquer sistema de ancoragem utilizado para garantir a segurança do trabalhador.
Escolha da Equipamento Certificado: Utilizar equipamentos de medição e teste adequados, como uma célula de carga, que é um dispositivo que mede a força de tração aplicada durante o teste.
Verificação dos Equipamentos: Todos os EPIs (Equipamentos de Proteção Individual) devem ser verificados antes da realização do teste, como os cintos de segurança, talabartes e outros.
2. Execução do Teste
Posicionamento da Célula de Carga: Conectar uma célula de carga ao ponto de ancoragem a ser testado. A célula de carga deve estar posicionada de modo a simular a tração vertical que seria exercida em um ponto de ancoragem durante uma queda.
Aplicação Gradual de Carga: A carga deve ser aplicada de forma progressiva, geralmente começando de maneira suave e aumentando até o limite especificado. Isso pode ser feito utilizando um sistema de cordas, guinchos ou outro dispositivo que permita a aplicação controlada da força.
Verificação da Estabilidade: Durante o teste, o ponto de ancoragem deve ser monitorado visualmente para identificar qualquer movimento ou alteração na estrutura que possa indicar falhas (descolamento, fissuras ou deformações). A carga é normalmente aumentada até que atinja o limite especificado pela norma ou até que a ancoragem mostre sinais de falha.
3. Interpretação dos Resultados
Resistência do Ponto de Ancoragem: O ponto de ancoragem é considerado seguro se resistir ao teste sem se deslocar ou falhar. Em alguns casos, a força máxima que o ponto de ancoragem deve suportar é determinada pela norma ou especificação técnica aplicável (por exemplo, 2.000 N para trabalhadores em alturas acima de 2 metros, dependendo da situação).
Falhas ou Defeitos: Caso o ponto de ancoragem falhe, a causa da falha deve ser identificada e corrigida. A falha pode ocorrer devido a instalação inadequada, material defeituoso ou desgaste excessivo.
4. Documentação e Ações Corretivas
Relatório de Teste: Após a realização do teste, deve ser elaborado um relatório detalhado com os resultados, indicando a carga aplicada, os métodos utilizados, a resistência do ponto de ancoragem e quaisquer falhas observadas durante o teste.
Correções Necessárias: Se o ponto de ancoragem falhar, ele deve ser substituído ou reforçado para garantir que esteja em conformidade com os padrões de segurança.
5. Periodicidade dos Testes
Testes Regulares: A NR-35 e outras normas de segurança recomendam a realização de testes periódicos, principalmente quando novos pontos de ancoragem são instalados ou após intervenções no sistema de ancoragem.
Testes Após Modificações: Sempre que houver modificações nas instalações ou nos pontos de ancoragem, novos testes devem ser realizados para garantir que as mudanças não comprometeram a segurança.
Normas e Exigências Relacionadas
NR-35 (Trabalho em Altura): A NR-35 exige que os pontos de ancoragem sejam devidamente projetados, instalados e testados de acordo com normas técnicas. A realização do teste de arrancamento estático é um dos métodos para garantir que os pontos de ancoragem atendam às exigências de segurança.
Norma ABNT NBR 15247 (Sistemas de Ancoragem): Esta norma estabelece os requisitos para a instalação e teste de pontos de ancoragem, incluindo os requisitos técnicos de resistência.
Conclusão
O Teste de Arrancamento Estático é fundamental para garantir que os pontos de ancoragem sejam seguros para o trabalho em altura, proporcionando proteção contra quedas. Ao realizar esse teste, você assegura que a instalação esteja em conformidade com as exigências de segurança e contribui para a criação de um ambiente de trabalho mais seguro.
A realização de testes regulares é uma medida preventiva importante, pois ajuda a identificar e corrigir possíveis falhas antes que se tornem riscos reais para os trabalhadores.
FALE CONOSCO
Estamos prontos para ajudar você
Entre em contato com a Athos Assessoria e Treinamentos!
- (11) 99557-1166